This tutorial will demonstrate pre-dimensioning of the geometry of a bevel gear stage according to ISO 23509. After pre-dimensioning, the bevel gear stage includes all information required for standard calculations and advanced local gear calculations. After the calculation is completed, the machine settings (Standard.KGD) can be exported.
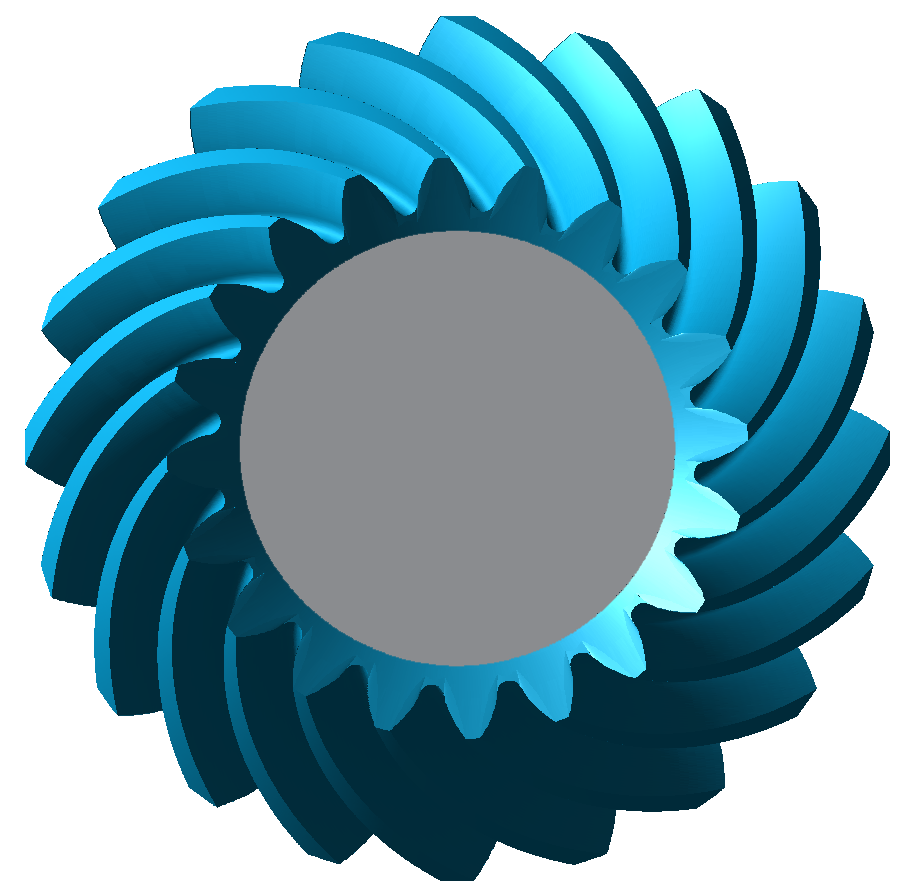
Create a new model
(Project → New)
Add a bevel gear stage
Right-click the Gear Unit in the Model Tree and add a new bevel gear stage component.
Specify the gear data
Enter the gear data in the assistant as shown in the image below.
Basic geometry information
Select "Bevel stage [3]" in the Model Tree, go to Calculations -> Single component calculations -> Geometry design acc. to ISO 23509 (2016). There are 3 separate tabs in the Editor for entering data. Start with the "basic geometry data" tab, and enter the parameters as shown below.
Tip
For more information on the different design methods, see the attribute help
for the attribute "ISO 23509 (2016) calculation method" in the basic geometry tab.
Tooth profile specifications
Switch to the "tooth profile" tab in the Editor and enter the parameters as shown below.
Microgeometry specifications
Switch to the "microgeometry" tab in the Editor and enter the parameters as shown below. Activate "show default values for crowning" and set the heat treatment and operating conditions. The corresponding default values for the profile crowning and, once the cutter module has been specified, depth crowning are shown as interval or standard values for orientation.
Start the calculation
To start the pre-dimensioning calculation, select "Bevel stage [3]" in the Model Tree and double-click "geometry design acc. to ISO 23509 (2016)" in the Calculations window.
Results
Under the "basic geometry data" tab in the Editor, you can see that the values for "mean helix angle" and "face width" have been calculated.
Notice
To export the machine settings data, right-click on the bevel gear stage and choose "Export Standard.KGD."
The calculated geometry can now be displayed in the 3D View
. Right-click in the 3D View and select "show fine geometry."