An Getriebe in der Antriebstechnik werden grundsätzlich folgende Anforderungen gestellt:
Ein Getriebe dient zur Leistungs- und Bewegungsübertragung. Dabei soll zusätzlich über die Übersetzung meist eine Wandlung von Drehmoment und Drehzahl stattfinden.
Die Leistungs- und Bewegungsübertragung soll möglichst gleichförmig sein und eine geringe Schwingungsanregung aufweisen.
Durch eine hohe Leistungsdichte (z.B. Drehmoment pro kg) soll eine Kosteneffizienz gewährleistet werden.
Die Leistungsübertragung soll einen hohen Wirkungsgrad aufweisen.
Die verwendeten Bauteile sollen einfach und in Serienfertigung herstellbar sein.
Die Betriebssicherheit muss hoch sein.
Für achsparallele Antriebe erfüllen evolventische Stirnradverzahnungen diese Anforderung in hohem Maße und werden deshalb dort überwiegend eingesetzt.
Die günstigen Eigenschaften von Stirnrädern lassen sich aus der evolventischen Form der Zähne ableiten. Diese lässt sich durch die so genannte Fadenkonstruktion erklären, bei der sich die Evolvente aus der Abwicklung eines Fadens von einem Zylinder ergibt.
Fadenkonstruktion einer Evolvente
(1) Evolvente
(2) Faden
(3) Grundkreis
Bei einem realen Zahnrad wird die evolventische Zahnflanke in gleicher Weise durch das Abwälzen eines Verzahnungswerkzeugs mit schräger Schneide (Eingriffswinkel α > 0) auf dem Teilkreis erzeugt. Dabei ergibt sich der Grundkreis, an dem die Berührnormale die Flanke tangiert, aus dem Teilkreis mal dem Kosinus des Eingriffswinkels.
Ein vollständiges Zahnrad ergibt sich dann aus dem Zusammenfügen mehrerer so erzeugter Evolventen in gleichmäßigen Abstand entsprechend der Anzahl der Zähne.
Je nach Größe der Zähne lassen sich unterschiedlich viele Zähne über dem Umfang verteilen. Als Maß für die Größe der Zähne ist der so genannte Modul(mn) definiert, welcher sich aus dem Teilkreis geteilt durch die Zähnezahl ergibt. Aus Zähnezahl und Modul ergibt sich dann dann die grundsätzlich Baugröße eines Zahnrades. Um für die Zahnform weitestgehend unabhängig von der Zähnezahl zu bleiben, werden Verzahnungsdaten, z.B. die Zahnhöhen, in vielen Fällen bezogen auf den Modul angegeben.
Stirnmodul
Normalmodul
Die Vorteile der Evolventenverzahnung ergeben sich aus den beschriebenen, konstruktiven Eigenschaften der Evolventenverzahnung, die den oben genannten Anforderungen an ein Getriebe entsprechen:
Stirnräder übertragen das Drehmoment durch Formschluß und besitzen damit eine hohe Leistungsdichte, eine geringe Reibung und damit einen hohen Wirkungsgrad sowie eine hohe Betriebssicherheit.
Da die Berührnormale der Evolvente immer den Grundkreis tangiert, ist die Zahnnormalkraft raumfest und zeigt für alle Eingriffstellungen immer entlang der Eingriffstrecke. Damit ergibt sich aus der Geometrie und Kinematik einer Evolventenverzahnung (ohne Betrachtung der elastischen Zahnverfromungen unter Last) keine Schwingungsanregung. Dies gilt auch bei Achsabstandsveränderungen durch Toleranzen oder Verformungen.
Die Kinematik der Abwälzbewegung kann im Herstellprozess mechanisch abgebildet werden. Damit ist eine relativ einfache Herstellung bei hoher Genauigkeit möglich. Es können Zahnräder mit unterschiedlichen Zähnezahlen mit dem gleichen Werkzeug hergestellt werden.
Die Geometrie und die Kinematik ist durch einfache Formelzusammenhänge beschreibbar, sodass absicherte und genormte Tragfähigkeitsnachweise verfügbar sind.
Üblicherweise werden die herstellrelevanten Verzahnungsdaten für das so genannte Bezugsprofil angeben. Dabei entspricht das Bezugsprofil der auf einem unendlich großen Durchmesser abgewälzten Verzahnung. Das Bezugsprofil ist damit zahnstangenförmig und besitzt gerade Flanken, wobei die Kopf- und Fußlinie des Bezugsprofils den Kopf- bzw. Fußkreisdurchmesser der Verzahnung tangiert, sodass die Zahnhöhe des Bezugsprofils der Zahnhöhe der Verzahnung entspricht. Genauso wie für ein Zahnrad lässt sich das Bezugsprofil auch für ein Herstellwerkzeug definieren. Das Bezugsprofil des Herstellwerkzeugs enstpricht dem Gegenstück der Verzahnungswerkzeugs. Es ist zu beachten, dass dabei der Zahnkopf des Verzahnungsbezugsprofils dem Zahnfuß des Werkzeugbezugsprofils enstpricht und umgekehrt.
(1) Bezugsprofil
(2) Kopflinie
(3) Fußlinie
Verzahnungsbezugsprofil | Werkzeugbezugsprofil |
Die Verwendung von Bezugsprofile soll die Anzahl der verwendeten Verzahnungswerkzeuge minimieren und liefert gleichzeitig durch das geradflankige Profil eine einfachere Definition der Geometriegrößen. Bezugsprofile für Verzahnungen im allgemeinen Maschinenbau sind in DIN 867 und für Verzahnungen in der Feinwerktechnik in DIN 58400 genormt. In der FVA-Workbench können auch von diesen Normen abweichende Geometrien definiert werden.
Die Bestimmung der Verzahnungsgeometrie von Stirnrädern basiert in der FVA-Workbench auf der Abwälzsimulation von ein oder zwei vorgegebenen Verzahnungswerkzeugen. Dies entspricht der oben geschilderten Kinematik bei der Erzeugung einer Evolvente. Bei Stirnrädern wird eine zur Wälzgeraden schrägstehende Schneide verwendet. Damit wird immer noch eine Evolvente erzeugt. Das Abwälzen erfolgt aber nicht mehr am Grundkreis sondern am Teilkreis. Der Teilkreisdurchmesser ergibt sich damit zu:
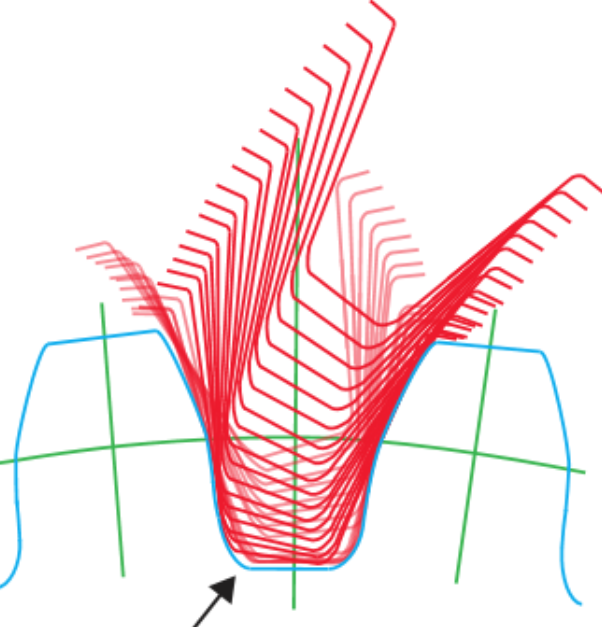
Abwälzkinematik bei der Zahnradherstellung
In der FVA-Workbench können für die Vor- und Fertigverzahnung sowohl gradflankige Werkzeuge (wie z.B. Fräser, Hobelkämme) oder evolventische Schneidräder nach DIN 3960 definiert werden.
![]() Gradflankiges Werkzeug mit (links) und ohne (rechts) Kantenbrechwinkel αKn0. | ![]() Gradflankiges Werkzeug mit Protuberanz |
Schneidrad ohne Kantenbrechflanke und Kopfkantenbruch (links) Schneidrad mit Kantenbrechflanke und Kopfkantenbruch (rechts) | Schneidrad mit Protuberanz und Kopfabrundung |
Die Beschreibung der Werkzeuge erfolgt dabei über die Eingabe der Daten des Werkzeugbezugsprofils. Da das Bezugsprofil des Verzahnungswerkzeugs das Gegenprofil zum Verzahnungsbezugsprofils darstellt, ist zu beachten, dass die Zahnkopfhöhe des Werkzeugbezugsprofils der Zahnfußhöhen des dazugehörigen Zahnrades entspricht und umgekehrt. Es ist darüber hinaus möglich, eine von der Profilbezugslinie abweichend Messlinie zu definieren, auf die sich die eingegeben Werkzeughöhen beziehen.
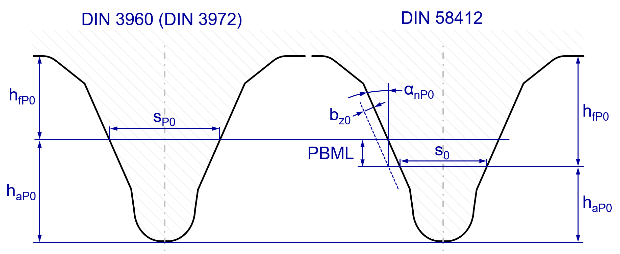
Bestimmungsgröße des Werkzeugbezugsprofiles
Neben den Werkzeughöhen ist die Kopfabrundung des Verzahnungswerkzeugs vorzugeben. Hier kann auch die automatische Bestimmung eines vollausgerundeten Werkzeugkopfs ausgewählt werden.
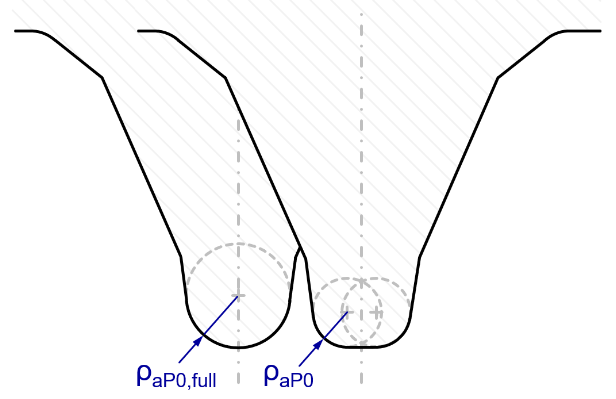
Werkzeugkopfabrundung
Wird ein Zahnrad durch zwei Abwälzvorgänge hergestellt, ergibt sich durch den Schleifabtrag beim Fertigverzahnen eine Kerbe im Zahnfuß. Dies kann durch die Vorgabe einer Protuberanz am Vorverzahnungswerkzeug verhindert werden. Durch die Verbreitung des Werkzeugkopfs wird beim Vorverzahnen ein Unterschnitt erzeugt, der dann dafür sorgt, dass das Fertigverzahnungswerkzeug nicht in Kontakt mit der Zahnfußausrundung kommt. Wenn Protuberanzbetrag in der gleichen Größenordnung liegt wie der Schleifabtrag, kompensieren sich beide Effekte.
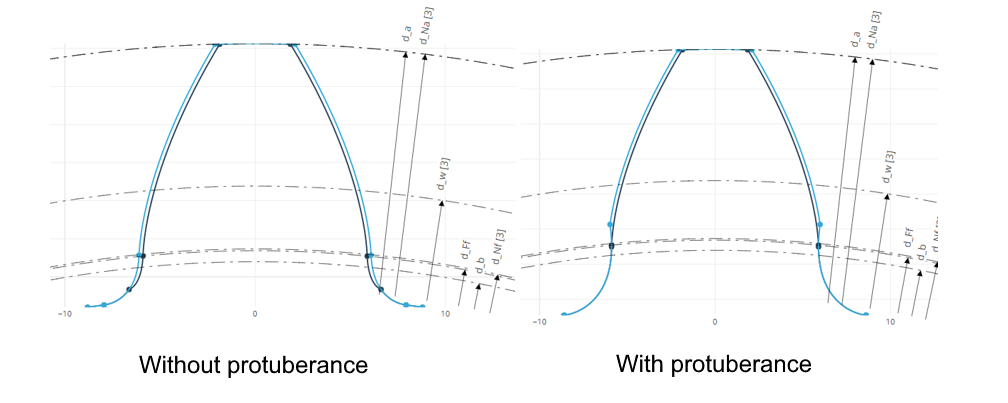
Zahnprofil mit und ohne Protuberanzwerkzeug
Die Zahnfußausrundung wird durch den Werkzeugkopf erstellt, wobei die Werkzeugkopf eine so genannte Trochoide (Schleifenevolvente) beschreibt. Für Verzahnungen ohne Unterschnitt schließt sich die Zahnfußausrundung tangential an die Flankenevolvente an.
(1) Werkzeug
(2) Evolvente
(3) Wälzgerade
(4) Teilkreis
(5) Zahnfußausrundung
(6) Werkzeugkopfrundung
Bei sehr kleinen Zähnezahlen, stark negativen Profilverschiebungen oder bei der Verwendung von Protuberanzwerkzeugen wird ein Unterschnitt erzeugt, sodass kein tangentialer Übergang zwischen der Flankenevolvente und der Zahnfußausrundung mehr vorliegt. Wir der Unterschnitt zu groß, so führt dies zu einer Reduzierung des Zahnfußquerschnitts und damit zu einer Schwächung des Zahnfußes sowie zu einer Verkürzung der Evolvente.
In diesen Fällen kann durch eine Verkleinerung der Werkzeugkopfhöhe oder eine positivere Profilverschiebung Abhilfe geschaffen werden.
Über die Wahl der Profilverschiebung kann bestimmt werden, aus welchem Bereich der Evolvente die Zahnflanke besteht, indem die Profilbezugslinie (auf die sich die Zahnhöhen beziehen) um den Betrag der Profilverschiebung verschoben wird.
Bei gegebener Profilverschiebungssumme lassen sich die Profilverschiebungen in der FVA-Workbench nach folgenden Kriterien automatsich bestimmen:
Empfehlung nach DIN 3992
Gleiche Zahnfußspannung
Gleiche maximale Gleitgeschwindigkeiten
Gleiche Wälzpressung
Neben diesen Kriterien können die Profilverschiebungen auch über die Vorgabe folgender Prüfmaße definiert werden:
Zahnweite und Messzähnezahl
Diametrales Maß und Messkugeldurchmesser
Zahndickensehne und Höhe über der Zahndickensehne
Der Kopfkreisdurchmesser von Stirnädern ist meist bereits durch den Außendurchmesser des zu bearbeitenden Werkstücks vorgegeben und wird üblicherweise nur bei kleinmoduligen Verzahnungen direkt mit dem Verzahnungswerkzeug gefertigt. Neben der Bestimmung des Kopfkreises durch das Werkzeug und als Direkteingabe lässt sich der Kopfkreis in der FVA-Workbench auch automatisch nach DIN 3960 oder DIN 867 oder durch Vorgabe eines Kopfhöhenfaktors ermitteln. Grundsätzlich lässt sich mit einem größeren Kopfkreisdurchmesser eine größere Überdeckung erreichen, wobei dies durch folgende Kriterien begrenzt wird:
Minimale Zahndicke am Zahnkopf sa. Durch eine zu geringe Zahnkopfdicke wird dort der Zahnquerschnitt reduziert, was zu einem Abbrechern der Zahnköpfe führen kann. Bei randschichtgehärteten Verzahnungen kann es darüber hinaus zu einer lokalen Überhärtung kommen, was die Bruchgefahr weiter erhöht.
Minimales Zahnkopfspiel. Es muss eine minimale Abstand des Zahnkopfes zum Zahnfußkreisdurchmesser des Gegenrades gewährleistet bleiben, damit es dort auch bei ungünstigen Toleranzlagen nicht zu einem Kontakt kommt.
Eingriffsstörungen im Zahnfuß des Gegengrades. Abhängig von der Zahnfußgestaltung des Gegenrades kann es bei einem zu großen Kopfkreisdurchmesser auch zu einem Kontakt in der Zahnfußausrundung oberhalb des Fußkreises kommen.
In der FVA-Workbench werden diese Bedingungen unter Berücksichtigung der vorgegebenen Toleranzen und der lastabhängigen Verformungen des Getriebesystems abgeprüft und es erfolgt eine entsprechende Warnmeldung an den Benutzer.
Die für Stirnräder zulässigen Toleranzen werden durch die Vorgabe der Verzahnungsqualität bestimmt. Die entsprechenden Abweichung sind in folgende Gruppen gegliedert:
Profilabweichungen
Flankenlinienabweichung
Zahndickenabweichungen
Teilungsabweichungen
Rundlaufabweichungen
In der FVA-Workbench können diese Abweichungen entsprechend Ihrer Verzahnungsqualiät nach ISO 1328 (1995 und 2013) sowie nach DIN 3960 berechnet und ausgegeben werden.
Für die meisten Anwendungen muss auch bei ungünstigen Toleranzlagen sichergestellt sein, dass genügend Rückflankenspiel vorhanden ist, um ein Klemmen der Verzahnung zu verhindern. Dies wird durch die Definition von geeigneten unteren und oberen Zahnweitenweitenabmaßen für die Fertigung erreicht. In der FVA-Workbench können dazu die in DIN 3967 angegeben Abmaß-Toleranzreihen ausgewählt oder auch benuzterspezifische Werte eingegeben werden. Das minimale und maximale Flankenspiel ergibt sich dann durch dieses Zahnweitenabmaße in Kombination mit der Toleranz des Achsabstands. Die Achsabstandsabmaße können dabei über die Vorgabe des Toleranzgrades für das Toleranzfeld je nach DIN 3964 oder als Direkteingabe bestimmt werden. Zusätzlich wird überpüft, wie sich der Achsabstand und damit das Flankenspiel durch elastische Verformungen im Getriebe ändert. Reduziert sich das Flankenspiel bis auf Null, wird eine entsprechende Warnung ausgegeben.
In der Praxis ist es wichtig, dass die gefertigten Zahnräder auch den rechnerisch geforderten Toleranzen entsprechen. Dies kann über die folgenden, bereits bei der Definition der Profilverschiebung angesprochenen, Prüfmethoden ermittelt werden:
Die zulässigen Minimal- und Maximalwerte für die einzelnen Messungen werden von der FVA-Workbench anhand der vom Benutzer vorgegeben Abmaße automatisch berechnet und ausgegeben. Dabei ist es möglich, für die Messmittel benutzerdefinierte Werte abweichend zu DIN 3960 vorzugeben. Für die Messung der Zahnweite kann die Messzähnezahl und für der Messung des Diametralen Maßes der Durchmesser des Messstücks vom Benutzer angepasst werden.
Obwohl bei der Zahndickenmessung der Messwert direkt bestimmt wird, ist dieses Verfahren oft ungenau, da in vielen Fällen der Kopfkreisdurchmesser, welcher die Höhe der Messposition auf dem Profil bestimmt, relativ grob toleriert ist.