Hydrodynamic plain bearings can be considered in the FVA-Workbench with different levels of detail. When adding them to the model, a distinction is first made between radial and axial plain bearings:
Detail | Radial plain bearings | Axial plain bearings |
---|---|---|
Low | Linear stiffness | Linear stiffness |
Medium | Plain bearing tables | - |
High | Plain bearing co-simulation | Plain bearing co-simulation |
Linear stiffness
Lowering and tilting rigidity can be specified for the bearing position in the overall mechanical system. By default, the bearing is radially stiff and axially soft. Furthermore, the bearing width and the inner and outer diameter can be also specified for coupling with FEM structures. Following a system calculation, an optional detailed plain bearing simulation can be performed using the bearing reaction force determined in the system.
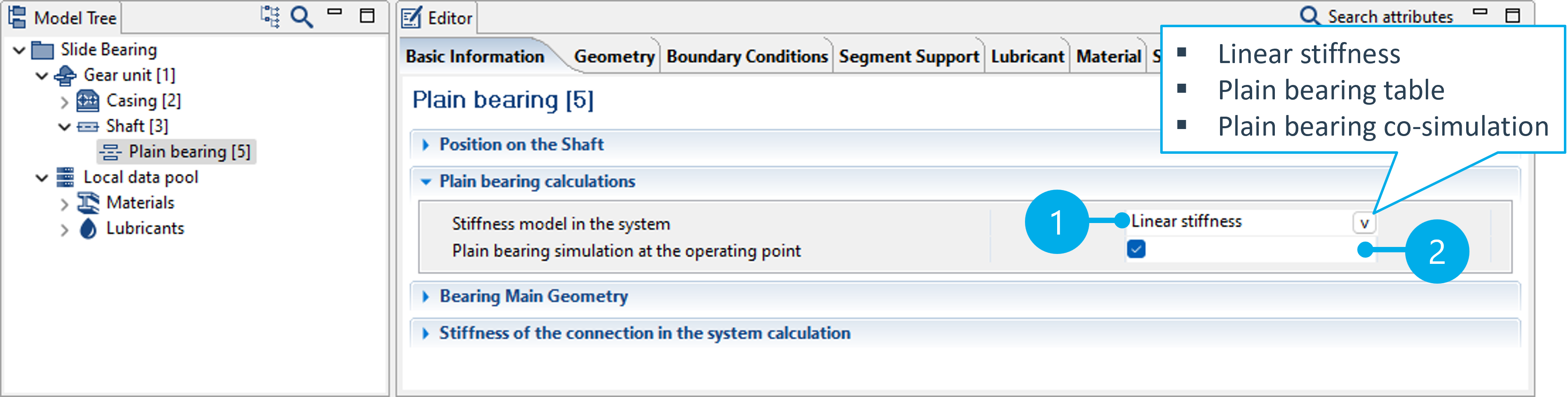
The level of detail can be selected in the Editor (1). A plain bearing simulation (2) can be performed after a system calculation.
Plain bearing tables
This calculation method uses dimensionless stored tables to approximate the operating behavior of radial plain bearings to achieve a good compromise between accuracy and calculation time, assuming the validity of the similarity theory. These tables were created within FVA Research Project 668 II based on DIN 31657.
Compared to a rigid analysis of the plain bearing with subsequent detailed simulation, the plain bearing tables are significantly better at representing the system behavior. In some cases, the determination of the bearing load and load distribution are also improved and the plain bearing losses can be considered in the overall system.
Tables are available for fixed segment, tilting pad, and offset-halves bearings. Key relevant parameters must be specified depending on the design such as the number of segments, the profiling, or the segment enclosure angle. Following a system calculation, an optional detailed plain bearing simulation can be performed using the bearing reaction force determined in the system.
Plain bearing co-simulation
Enables detailed modeling and simulation of radial plain bearings according to FVA 577. The underlying thermo-elasto-hydrodynamic calculation model was developed at the TU Clausthal ITR and validated in numerous test rig experiments. The bearing is considered in the overall system as part of a co-simulation; i.e., the stiffness behavior of the bearing is simulated in detail for the current operating point in each iteration step. However, the high-quality results of this variant requires significantly longer calculation times than other levels of detail.
Linear stiffness
Makes it possible to specify the stiffness at the bearing position in the overall mechanical system. By default, the bearing is rigid in the axial direction. Furthermore, the bearing width and inner and outer diameters can be specified for coupling with FEM structures. A detailed plain bearing simulation can also be performed following the system calculation based on the bearing reaction force determined in the system.
Plain bearing co-simulation
Enables detailed modeling and simulation of the axial plain bearing according to FVA 668. The underlying thermo-elasto-hydrodynamic calculation model was developed at the TU Clausthal ITR and validated in numerous test bench trials. The bearing is considered in the overall system as part of a co-simulation; i.e., the stiffness behavior of the bearing is simulated in detail for the current operating point in each iteration step. The results of this variant are of much higher quality, but this comes at the cost of significantly longer calculation times.