In braced drivetrains, part of the power transmitted in the gear meshes circulates within the gearbox and is not transferred from the input to the output. This type of system is used in drivetrains in which zero backlash is important, or in test benches in which the reference torque is applied by the bracing and only the power loss is transmitted by the drivetrain. The bracing is typically provided via mechanical or hydraulic load clutches.
This simplified model demonstrates how to design braced drivetrains in the FVA-Workbench.
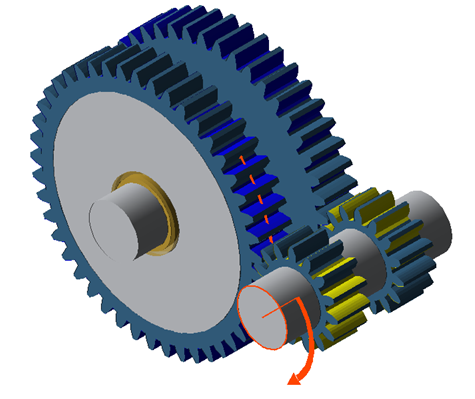
Example model of a braced drivetrain
Create a new model (Project → New)
Right-click on the gear unit in the Model Tree, choose "add component," and then select "Cylindrical stage."
Adjust the position of the gears in the wizard, as shown in the image below. New shafts will automatically be created for Gear 1 and Gear 2.
Right-click "Shaft [4]" in the Model Tree, choose "add component," and then select "Cylindrical stage."
Adjust the position of the gears, as shown in the image below. Select the output shaft (Shaft [6]) for Gear 2.
Right-click Gear 2 of the 1st cylindrical stage and convert it to an idler gear.
Notice
When a cylindrical gear is converted to an idler gear, it is positioned on a newly created auxiliary shaft which approximately corresponds to the wheel body.
A rolling bearing and coupling are added between this auxiliary shaft and the original shaft for transmitting the supporting forces and moments. The torque is transmitted via the coupling.
In this case, the transmission of torque by the coupling must be deactivated in the shift matrix of the Power Flow editor.
Right-click to rename each component as shown in the image.
Right-click "Output shaft" in the Model Tree and add a rolling bearing component.
Set the position of the bearing to be added as shown in the image below.
Set the position of the first bearing that was created earlier ("Rolling bearing [26]") as shown in the image below.
Change the stiffness of the coupling between the output shaft and the gear shaft ("Coupling [27]") as shown in the image below.
Click in the power flow editor to add the following load components to the gear unit:
1x load component on the input shaft; this represents the drive torque of the gear unit.
2x load components on the output shaft. The moment at the end of the shaft is the output torque of the gear unit. This is automatically calculated. The moment under Gear 2 of the first stage is the load torque that is applied to the second stage of the gear unit.
1x load component on the wheel shaft. The moment on the wheel shaft is the moment which acts against the load torque, which is applied to the first stage.
As described previously, the torque transmission of the coupling must be deactivated in the switching matrix.