Hydrodynamic radial plain bearings can be considered with different levels of detail in the FVA-Workbench:
Plain bearing tables

Orientation - when to use each calculation method
When "plain bearing table" is selected, the operating behavior is approximated based on predefined dimensionless tables, assuming the validity of the simulation theory. These tables were developed in FVA Research Project FVA 668 II based on DIN 31657, and integrated into the FVA-Workbench in FVA Research Project 961. In many cases, this variant is a good compromise between calculation speed and accuracy. The plain bearing tables can be considered in the overall mechanical system in the FVA-Workbench. Optionally, a detailed plain bearing simulation can be performed following the system calculation using the bearing reaction forces determined in the system.
Inputs
Only a few parameters are required for consideration of bearing tables for a bearing position. Characteristic diagrams are available for fixed segment, tilting pad, and offset halves bearings. Some relevant parameters (for example, the number of segments, profiling, or segment enclosure angle) are required, depending on the design.
The user can select between isothermal calculation (lubricant viscosity determined by the feed temperature) or an estimation of the effective temperature based on the friction loss and the (user-specified) lubricant throughput.
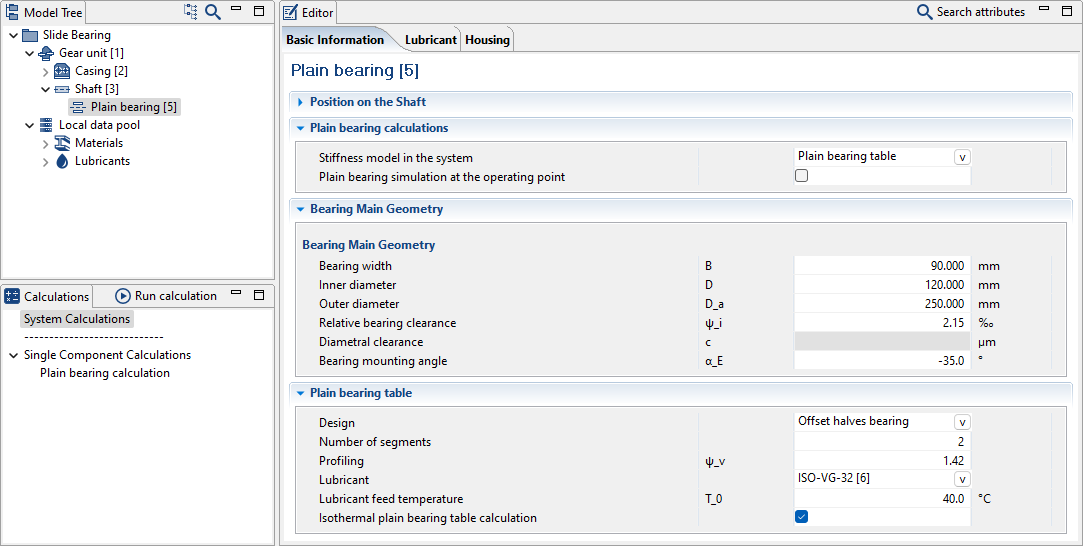
When the system calculation is started, a suitable bearing-specific table is created/interpolated from the stored tables based on the input parameters.
Calculation process
Within the system calculation, the operating conditions must repeatedly be determined for each bearing using the currently calculated displacements. The parameters relative displacement ε and displacement angle β are determined and used to determine various associated dimensionless parameters (Sommerfeld number, etc.) based on the bearing-specific table.
If isothermal calculation is selected, the effective (lubricant) temperature corresponds to the feed temperature. Otherwise, it is assumed that 100% of the friction power in the bearing is dissipated via the lubricant and an iteration is performed to determine the effective lubricant temperature and viscosity. The following parameters can ultimately be determined using these values:
Reaction forces
Tilting moments
Jacobian matrix
Friction torque
Power loss
Minimum lubricating gap thickness
Sommerfeld number
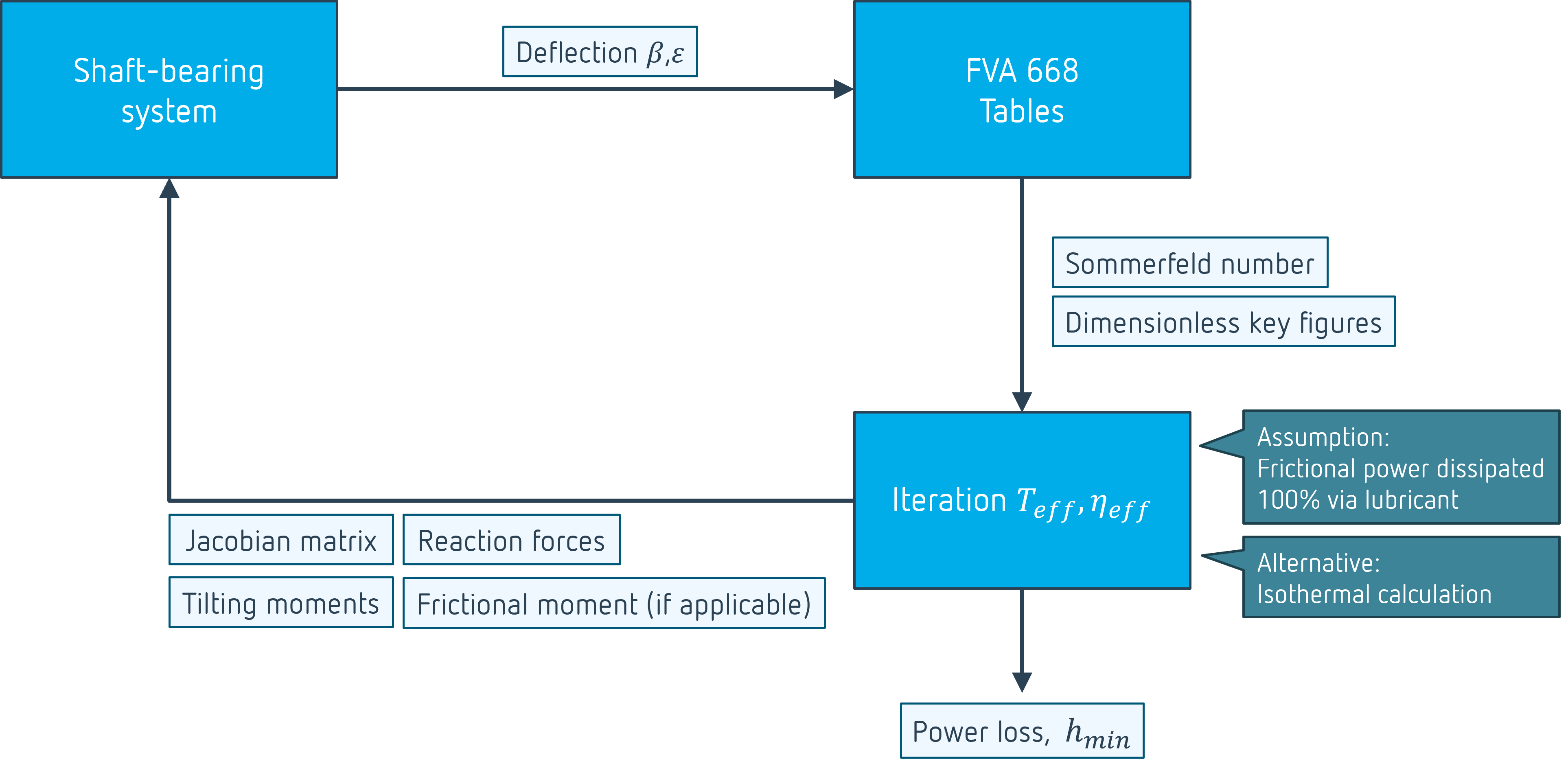
Calculation process when using plain bearing tables
Limitations
The characteristic diagrams from FVA 668 II were determined using isothermal calculations:
Limited accuracy when temperature is considered,
User specification of the lubricant flow rate is required for iteration of the effective temperature.
The characteristic diagrams from FVA 668 II were determined without tilting:
Tilting stiffness is considered linearly,
Influence of the tilt on the minimum lubricant gap thickness is not considered.
Only bearings whose characteristic parameters lie within the range of the predefined tables can be calculated (e.g., width-diameter ratio must be between 0.5 and 1.0).
Suggestions for extension of the tables can be submitted to customer support.
Sources
DIN 31657-1 Plain bearings - Hydrodynamic plain journal bearings under steadystate conditions - Part 1: Calculation of multi-lobed and tilting pad journal bearings
FVA 668 II Durchgängige Berechnung gleitgelagerter Welle-Lager-Systeme (Continuous calculation of shaft-bearing systems with plain bearings). Issue 1282, 2018